Not all Nickel is created equal - why "clean" nickel is vital
- Matthew Reynolds
- Mar 22, 2022
- 4 min read
Updated: May 25, 2022

In July 2020 Elon Musk said on an earnings call “Tesla will give a giant contract for a long period of time to any company who will mine nickel efficiently and in an environmentally sensitive way”
This had the effect of a lightning rod for global investors to look at Nickel companies and Nickel production.
The market demand for Nickel is expected to increase dramatically over the next few years, from about 2.2 million tonnes in 2020 to 3.5 million in 2030. Whilst Nickel required for EV batteries is also expected to soar by 64% to 2025 and represent around 31% of the demand by 2026.
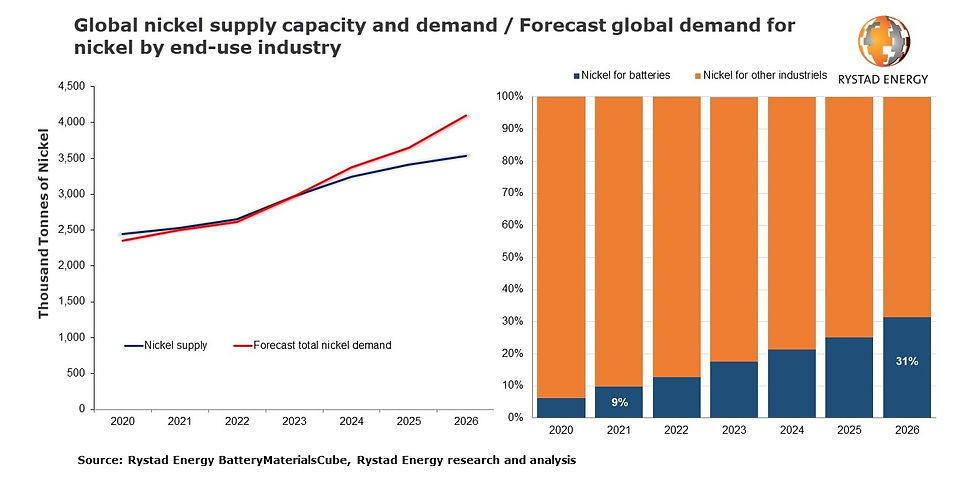
The big challenge – as posed by Elon Musk - is to nearly double supply with environmentally friendly and sustainable processes and with strong ESG metrics.
In addition, Nickel is one of the most technically difficult metals to process and refine with operations being different depending on ore deposit such as sulphide, oxide, laterite, or komatiite. The input type of ore determines the use of chemicals, Co2 emissions and greenhouse gas emissions.
There is growing global demand for producers to step-up and use electric vehicles on site, renewable power and to create positive social impact in the communities in which they operate through employment, healthcare, and education. The ability of Nickel producers to rise to these challenges and demonstrate strong ESG commitments and traceable, sustainable supply chain will enable them to pitch the product as “clean Nickel”.
We are seeing increasing relationships and partnerships in the Nickel value chain which assist ensure due-diligence and monitoring of the supply chain to assess compliance with recycling, traceability, ethical labour contracts and workers protection. Some of these partnerships include BHP and Tesla, Umicore and BMW, and Eramet and Suez.
EV batteries require Class 1 Nickel. This is Nickel that is that contains a minimum of 99.8% nickel. Class 2 Nickel is mostly used for Steel production and contains less than 99.8% Nickel.
Only about 46% of the world’s Nickel production is Class 1.
The global production of Nickel is dominated by Indonesia, Philippines, and Russia. Indonesia has experienced supply issues recently as the Government has announced measures to drastically reduce exports to preserve their resource base. Their proven resource base has been estimated to last only another 7-8 years.
Indonesia accounts for 26% of the world’s supply of Nickel. Indonesia also has the problem its production is highly energy intensive, and this energy comes from coal fired power plants with the highest carbon footprint of all energy forms.
Russia supply chains will also be problematic after their invasion of Ukraine and imposition of global sanctions. Russia currently accounts for about 11% of global supply.

Automakers and other end users of Nickel have begun buying direct from mining companies. As Markus Duesmann, the CEO of Audi said in early March 2022 “raw materials are going to be an issue for many years to come”.
There is also the possibility of recycling Nickel from end-of-life batteries, which will be accelerated by EU legislation and company commitments to ESG.
The supply constraints from Indonesia and Russia and increased demand for sustainable, ethical, and traceable Nickel will create significant opportunities for companies in the Nickel sector.
Two Australian based companies that may be likely to benefit from these developing tailwinds are Nimy Resources Limited and Neometals Ltd.
Nimy Resources Limited (ASX: NIM; FSE: P4G)
Nimy Resources Limited (ASX: NIM; FSE: P4G) is an ASX listed (dual-listed in Germany) Nickel explorer based in Western Australia.
The company listed via an IPO on the ASX on 22 November 2021 and was dual listed in Germany on 24 February this year.
The company has a strategy to explore for, extract and supply responsibly sourced and premium-priced nickel, with minimal impact to the environment and consultation and engagement with local communities.
Nimy resources is a first mover in a major new Nickel Sulphide belt covering a land area of 1,761 sqkm in a Tier 1 resource. Nimy resources has an extensive exploration program planned to explore and develop a pipeline of targets.
Nickel is key component of lithium-ion batteries and energy storage systems. At present this accounts for around 7% of demand. This is expected to grow to 31% by 2030.
Australia is the largest holder of economic nickel resources in the world with about 25% of global resources. The company is also fortunate to have a large-scale globally respected producer nearby in BHP Nickel. In July 2021, BHP announced a Nickel supply agreement with Tesla. The BHP refinery is one of the most sustainable and lowest carbon emission producers in the world and offers smaller explorers such as Nimy Resources a direct sales path to companies like Telsa Inc – the world’s largest manufacturer of electric vehicles and battery storage systems.

Neometals Ltd (ASX: NMT; FSE: 9R9)
Neometals Ltd is an ASX (dual-listed in Germany) listed company, developing opportunities in minerals and advanced materials essential for a sustainable future. The company has partnered with German engineering giant SMS group to form a Joint Venture “Primobius” to commercialise an environmentally friendly recycling solution for end-of-life and scrap lithium-ion batteries.
Primobius uses an advanced recycling process with low CO2 emissions to delivery high purity chemicals back to the battery manufacturing sector.
The recycling process consists of 2 stages
1. Shredding and beneficiation to physically separate components and remove metal casings, electrode foils and plastics from the main battery materials; and
2. Leaching, purification, and precipitation to produce refined chemical products from the hydrometallurgical processing facility.

The March 2022 Investor Presentation for Neometals Ltd can be uploaded below.
The goal of the Primobius process is to replace materials usually supplied by primary refiners by generating the finished cathode intermediates used by cell-makers.
A commercial scale processing plant handling 50 tonnes of batteries per day would generate a basket of low-value products such as plastic and metal casing – plus about 10,000 tonnes per year of Nickel sulphate, 3,340 tpy of lithium sulphate, 1,370 tpy of cobalt sulphate and 1,860 tpy of copper foil.
Below is a photo of the demonstration plant in Germany with the front-end shredder.
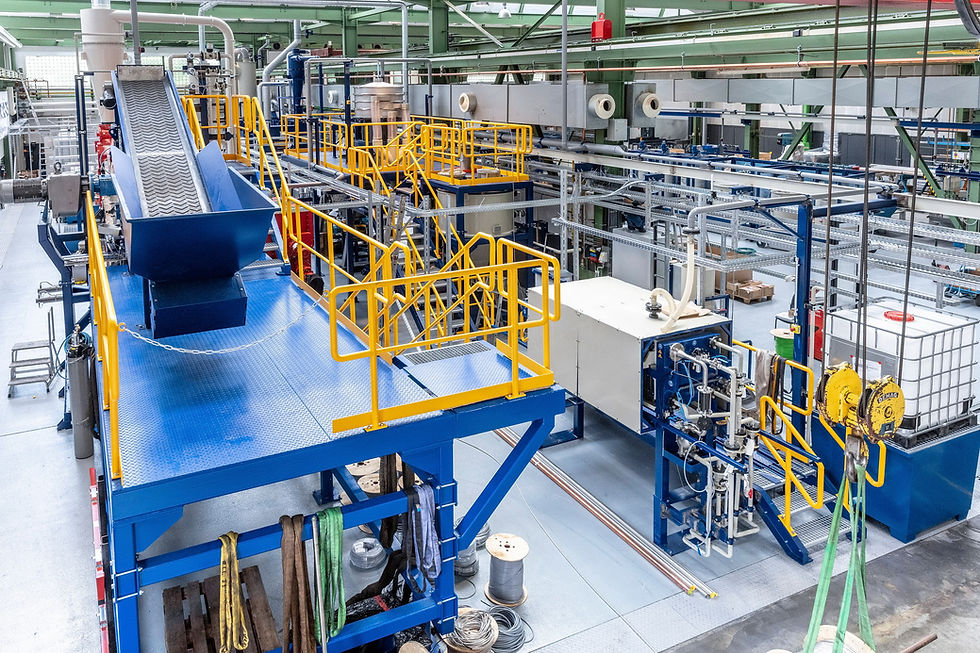
Earlier this month, Primobius announced it will work with Mercedes Benz to create a battery recycling plant at Mercedes operations in Kuppenheim, Germany. Neometals expects the plant will have a capacity of 2,500 tonnes per annum and the recovered material will be fed back to the recycling loop to produce more than 50,000 battery modules for the Mercedes EQ (Electric Intelligence) range of vehicles.
Below is another photo of the demonstration plant, this one of the hydrometallurgical process.
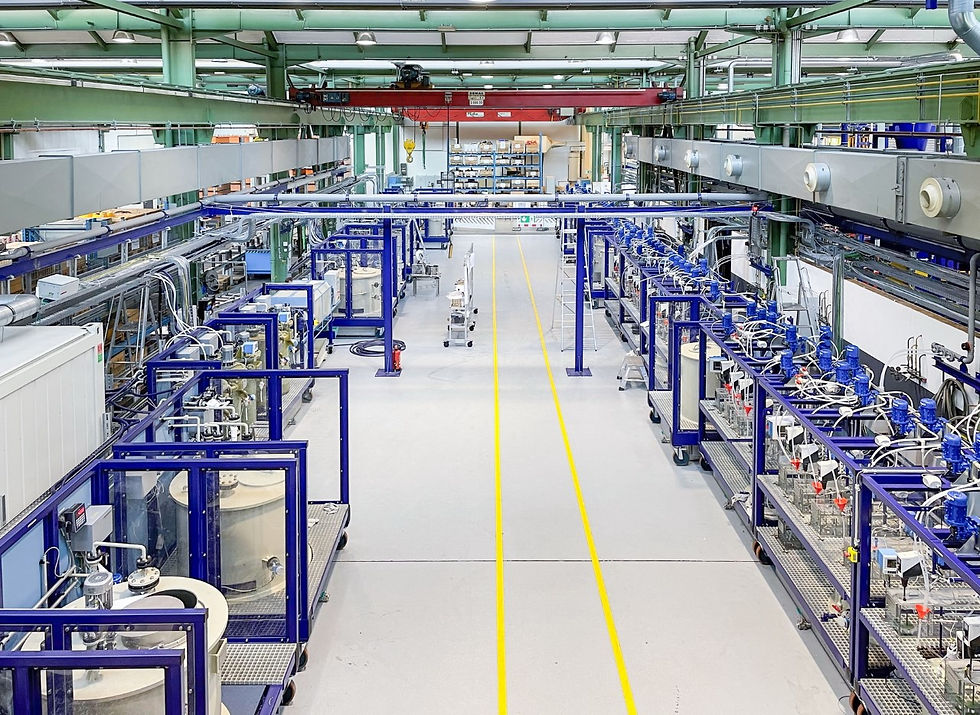
コメント